Market volatility, economic complexity, and unexpected costs, plus the ever-present shadow of uncertainty, are all factors that can inhibit an organisation’s ability to build a risk-proof business. Staying on track and within compliance and regulatory lines can be difficult in tough times, but with standardisation principles, companies can put the right bolsters in place to mitigate risk and enhance efficiencies.
RELATED: Using standardisation to successfully meet tender requirements in South Africa
“Building operational efficiency asks that the company focus on its culture and governance,” says Muhammed Ali, Managing Director at World Wide Industrial Systems Engineers (WWISE). “Once you have a thorough understanding of your existing culture through a gap assessment, you can then determine what level of technology to introduce and how you can more carefully align your governance and structure. And each of these elements contributes to an operational efficiency framework that can help you achieve your business objectives and implement strategies.”
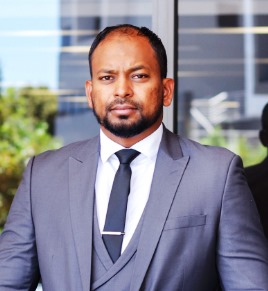
Muhammad Ali
A gap assessment is an ideal starting point for companies looking to find the right solutions that fit seamlessly within their environments. Using the insights provided by the assessment, you can create process maps rather than adhering to outdated procedures, and you can even use images, videos, and media to embed the culture of these new processes and approaches within the culture of your organisation. The ISO 9001:2015 QMS provides the organisation with the top management KPIs that can be used to undertake these assessments and implement these procedures meticulously – and can help your business frame its efficiency imperatives more clearly.
“The ISO 9001:2015 standard essentially outlines the requirements for a quality management system that ensures the consistent delivery of products and services that meet customer and regulatory requirements,” says Maylee Hartzenburg, Project & Operations Manager at WWISE. “It covers areas such as customer satisfaction, process improvement, and risk management so companies can continuously improve their QMS and gain a competitive advantage in the market. It’s a systematic approach to quality management that helps companies build strong foundations in uncertain times.”
Implementing this ISO is not as complex as many organisations believe. Many companies have a culture of fear around audits but shifting to this ISO standardisation is about continuous improvement and enhancing the overall business efficiencies in ways that benefit everyone.
“It can be tough to implement at first,” says Ali. “Many employees feel that everything is right. The philosophy of practicing the wrong thing and being the master of the wrong thing is difficult to change when people have been doing the same thing for a long time. But the benefits are instant and measurable. Certification is a feather in the company cap as it offers customers immense assurance and peace of mind, alongside optimum product and service delivery, and it improves revenue generation.”
Once the system has been implemented employee morale also changes as people become more aware of their roles and responsibilities and have the right tools to perform these roles to the best of their abilities. It helps organisations overcome unprofessional and inconsistent reporting, unverified documentation across essential areas of the business such as policies and procedures, and limited verification and validation. There are also the risks that come with non-standardisation that include poor supplier performance, dissatisfied clients and multiple forms that have the same purpose with poor visibility.
“Implementing ISO 9001:2015 can improve a company’s overall performance by enhancing customer satisfaction and improving process efficiency,” says Hartzenburg. “By implementing the standard, companies can create a culture of continuous improvement that bypasses the standard resistance to change and allows people to become more engaged with the business and its objectives.”
While standardisation may seem daunting, it is a proven approach to managing quality that has tangible and measurable returns on your investment. Whether it’s the time spent by your people adapting to new systems, or the shift in culture, or the ways in which you engage with your customers, the work put into achieving this certification is reflected in revenue, growth and market share.